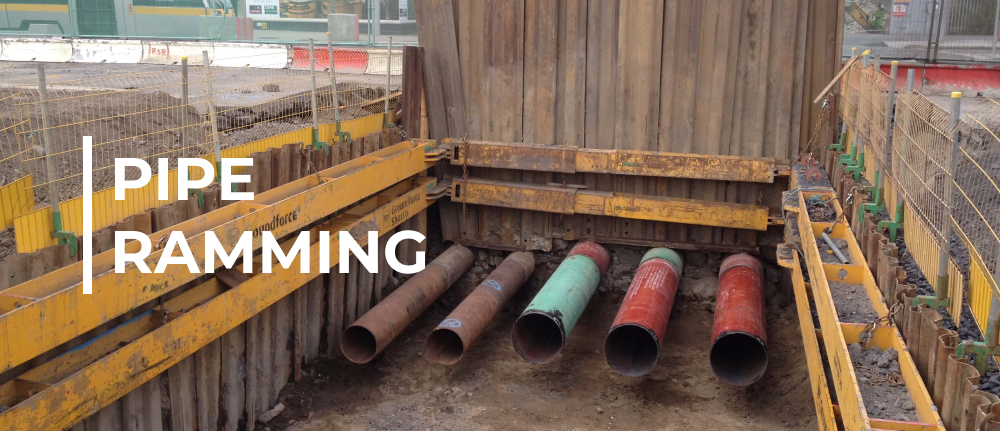
Pipe Ramming
Pipe ramming is a method of trenchless installation whereby a steel duct is installed under a particular obstacle such as road, rail, canal, river etc. The technique involves driving an open ended steel pipe through the ground by means of a pneumatic hammer.
When the pipe is installed the material is removed from the inside. As a result, there is no risk of loss of ground during the works. The only displacement is the wall thickness of the pipe + 10mm for the cutting shoe.
The time taken to complete the crossing will vary depending on the diameter of the pipe, the length of drive, and the ground conditions. Most crossings can be completed in one week. This method involves a non-steerable system and is not suitable for rock.
Pipe Ramming – The Process
Two pits are dug, one at either side of the crossing. The steel piping is usually in 6 or 12 metre lengths. There are no thrust walls or fixed abutments required. The driving pit needs to be 9 metres or 16 metres in length to accommodate the pipe and the hammer. A frame or runner is placed in the base of the driving pit onto which the first pipe length is lifted. A cutting shoe is welded to the front end of this pipe. This protects the end of the pipe from damage and with its hardened edge, will break any large cobbles or boulders
encountered. The runner is adjusted to the line level required.
Next the hammer is fitted to the end of the pipe and strapped into place. A series of concentric rings are used to fit the hammer to the various pipe sizes. The hammer is then connected to a compressor and driving can commence.
The volume of air delivered governs the rate of hammering. If the installation is for a sewer, it is crucial at this stage to check and adjust the level of the pipe. The first length is driven slowly until the pipe is established in the ground in order to maintain line and level.
Having driven the first pipe length the hammer is disengaged and the next length lifted into place and butt welded to the first length. Driving can then proceed at full speed. The normal rate of progress is about 6m an hour.
This process is repeated until the destination is reached. Having completed the drive the next step is to clean out the pipe. One method of doing this is to pressurise the pipe with a combination of air and water thus evacuating the spoil in one continuous core. An alternative method is to remove the spoil using an auger boring machine.